Replacing MDI with bio-circular materials
🡄 Go to sustainability overview
The share of MDI’s total carbon footprint is 51% (cradle-to-gate A1-A3).For example gas diffusion tight multi foil faced PIR. To reduce our carbon footprint, we’ve looked into ways to partially replace this MDI content with renewable bio-based feedstock. And with success: with Eurowall® Impact and Eurothane® Silver Impact we have developed an entire product line with 25% bio-circular content, cutting our carbon footprint by 43%*.
*Internal LCA calculation based on EN15804+A2 standard, for modules A1-A3 (cradle to gate), based on mass balance approach
Progress status
🚀 STAGE | Study 🡆 Lab test 🡆 Pilot trial 🡆LAUNCH 🡆 Upscale |
📈 NEXT STEP | Increase the % of alternative materials in our product range |
Blowing agent and additives are needed to produce our insulation boards. Our insulation boards are produced without the addition of harmful CFCs/HFCs.
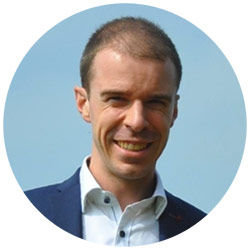
“We don’t wait for the EU Green Deal to impose obligations. We’ve already taken a head start, because we’re convinced the Mass Balance approach is thé way forward. We’re now working hard to have our carbon footprint validated in order to drive change in the industry.”
Project description
What is it?
Bio-circular content refers to waste and residues from biological origins, such as vegetable oil. Instead of sending them to landfill or turning them into lower-value energy, they are reused as or recycled into raw materials for new products, extending their lifetime and saving carbon emissions by reducing the need for virgin materials.
In partnership with Covestro, a leading producer of advanced polymers, we’ve found a way to turn biomass waste from agriculture into a sustainable alternative for MDI.
How do we do it?
The move from fossil-based to renewable and bio-based materials is a much-needed yet drastic transition. It doesn’t happen overnight. We therefore use the Mass Balance approach, mixing alternative materials from renewable bio-based sources with traditional fossil-based MDI. That way, we can gradually shift to bio-circular materials without having to set up separate production lines.
Mass balance means that the quantity of Impact products sold (output) has to be in balance with the quantity of biomass purchased (input). In other words, our total volume of bio-circular materials in production is linked directly to the success of our Impact line.
The result
We’ve successfully redeveloped Eurothane Silver® and Eurowall®, using 25% biocircular content. The result is a 43%* carbon reduction as compared to a traditional PIR board, for the same high-quality performance.
*Internal LCA calculation based on EN15804+A2 standard, for modules A1-A3 (cradle to gate), based on mass balance approach
Discover our Impact Line
25% bio-circular content, 43%* CO2 savings
*Internal LCA calculation according to EN15804+A2 standard, for modules A1 - A3 (cradle to gate), based on the mass balance method.